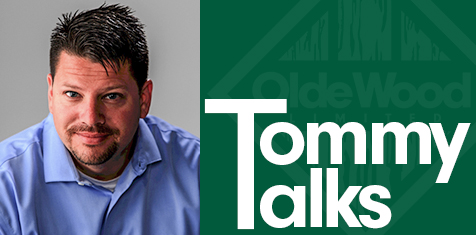
Tommy Talks: Prefinish - Best Business Practices
A few times each week Olde Wood Limited Owner Tommy Sancic sends out an audio recording of encouragement and education to employees. The following excerpt is a transcript of this week's "Tommy Talks".
Good afternoon, hope everyone is having a fantastic week! We're very excited that we've expanded our prefinished lines. Over the last 3 to 4 decades and even further back, unfinished flooring dominated sales and manufacturers generally did not make prefinished material available. However, that is changing and we recognize that the whole market is going to be comprised almost exclusively of prefinished material very soon. In order to keep ahead of the trends we asked ourselves some questions: How do we move in a direction that better suits our customers’ needs? What can we do to separate ourselves from our competition? Ultimately, how do we attack this market better and get ahead of the trend?
Our prefinish department has seen an increased volume of about between 15-20% annually. As we end the first calendar quarter, our projections show prefinished floors are going to comprise of about 65%, maybe upwards of 70% of our segment within the flooring market. Furthermore, we have evidence that in the next 12 to 24 months, prefinished floors are going to constitute 80-90% of what our customers are demanding. Turnkey products are the direction that we see the market is moving. Unfinished floors that require installation, sanding, and finishing on-site are understandably cumbersome. When a consumer sees an image or a sample and they say, “that's what I want”, that's what we want to give them.
We are headed in the right direction because we offer finishes that are eco-friendly and exhibit superior adhesion to our products. They don't off-gas VOC’s (volatile organic compounds). That means they are safe for the environment, our customers’ health, their home, and their family and pets. Some of the finishes that our competitors are applying to their products have a 20 to 40 year warranty. There's a reason why they can offer such a lengthy warranty and it’s because they add Aluminum Oxide to the finish, a chemical compound that adds substantial hardness and abrasion resistance but poses significant health hazards. The NFPA 704 is the government agency responsible for the “Standard System for the Identification of the Hazards of Materials for Emergency Response”. They’ve classified Aluminum Oxide as exuding the same health risks as Acetone and the primary exposure danger is contact with skin. In lay terms, the finish lasts longer than most homeowners will even live in that house but they should avoid touching it.
Pardon me while we collectively scratch our heads...
Over time, Aluminum Oxide off-gasses compounds so even with minimal skin contact, still poses risks. Researchers are just now finding that those compounds cause allergies and health risks.
At Olde Wood, we could offer a finished product with the same level of hardness but I (we) simply hold ourselves to a higher standard. Leadership here at Olde Wood has concluded that our customers’ health and wellness is and always will be our top priority. Secondary to health risks, we sell a unique and gorgeous product that we have designed to feel as real as it is. Coating it with multiple layers of a ceramic compound like Aluminum Oxide essentially turns that product into a piece of plastic with a thin layer of wood underneath. The value of our products comes from the feel and authenticity of each and every board and beam. Authenticity is not something we’re willing to compromise as it is the foundation of our product offering. Cutting corners isn’t consistent with our vision of providing consumers with high quality, antique reclaimed wood products.
I'd like to elaborate on one of the products that we use and that is our oil-based prefinish. It is extracted from plants. It is water resistant, penetrates the surface of the wood very well, and is VOC-free. It is NOT a maintenance-free product and since we sell with total transparency, I would stress how important is it that we let our potential customers know that. Maintenance meaning occasional dusting with a microfiber mop and applying our Wood-ZEE clean oil soap. In order to make it as easy as possible to maintain their floors, we formulated our own line of maintenance products. That way we have total control over how effective our maintenance recommendation is. Like our finishes, we formulated our cleaning products to be free of harsh chemicals and they are completely biodegradable. Since our finish products are organic-based, harsh chemicals can ruin the finish so certain cleaners with solvents like a combination of dish soap and water will likely ruin the finish.
As it pertains to finishes, our warranty covers adhesion to the surface of the wood. Again, we could add preservatives and hardeners to our finish and extend our warranty but we know that those compounds will eventually be prohibited for this type of use. This will likely force our competitors into costly redevelopment of their products and even worse, expose them to legal repercussions and a negative public perception. To the consumer that is shopping based on warranty I would contend that the health risks/costs associated with that type of product far outweigh the benefits. The bottom line is that we are always striving to create the most sustainable business practices and we firmly believe this is the best option for our prefinished products.
Again, I hope that these are informative and if you have any questions or comments, please reach out to me. I appreciate you all. Hope everyone has a great day and a productive week!